Die Fehlermöglichkeits- und Einflussanalyse (FMEA) ist eine systematische Methode, um potenzielle Fehler und Risiken in Produkten, Prozessen oder Systemen frühzeitig zu erkennen und deren Ursachen zu identifizieren. Sie ist branchenunabhängig einsetzbar und verfolgt das Ziel, systematisch Fehlerursachen auszuspüren, um Sicherheits- und Qualitätsanforderungen zu erfüllen und Fehler- sowie Garantiekosten zu minimieren. Die FMEA ist präventiv und korrektiv einsetzbar. Es gibt verschiedene Arten von FMEAs, darunter die System-FMEA, die Design-FMEA und die Prozess-FMEA.
Wenn Kunden aufgrund eines fehlerhaften Produkts unzufrieden sind oder das Produkt sogar gesundheitsschädlich ist, kann dies einen erheblichen Imageschaden nach sich ziehen. Auswirkungen, die einen unter Umständen jahrelang verfolgen oder sogar die Existenz des Unternehmens gefährden können. Mit einer Fehlermöglichkeits- und Einflussanalyse (FMEA) können solche Szenarien frühzeitig erkannt und Maßnahmen ergriffen werden.
Was ist eine FMEA?
Eine FMEA ist eine systematische Methode, mit der potenzielle Fehler und Risiken identifiziert und bewertet werden können. Systematisch deshalb, weil die Analyse einer Struktur folgt, die das gezielte Aufbauen von Fehlerketten ausgehend von der Produkt- bzw. Servicestruktur bis auf Ebene der Prozesse ermöglicht. Sie ist universell einsetzbar – egal ob für Prozesse, Produkte oder Systeme und unabhängig von der Branche. Korrekt eingesetzt können die Erkenntnisse aus der FMEA wertvolle Inputgeber sein für die Optimierung der Prozesse und Produkte / Services, um Kundenanforderungen, Sicherheitsvorgaben, Qualitätsrichtlinien und die Abwendung von Schäden zu ermöglichen.
Besuchen Sie auch unser Training „Prozesse aufnehmen, analysieren und verbessern“.
Welche Arten von FMEA gibt es?
Die FMEA kann sowohl präventiv – also zum frühen Zeitpunkt einer Produktentwicklung bzw. von neuen Prozessen eingesetzt werden und auch korrektiv bei bereits bestehenden Produkten und Prozessen. Im Wesentlichen sind drei Arten der FMEA relevant: Design-FMEA, Prozess-FMEA und die MSR-FMEA. Als weitere Ausprägung gibt es noch die System-FMEA sowie die Human-FMEA (menschliche Handlungsfehler) zur Untersuchung von Schnittstellen bzw. menschlichen Handlungen und deren Fehlerpotenzialen. In der Praxis am häufigsten eingesetzt werden die Design-FMEA und die Prozess-FMEA, sowie die MSR-FMEA als Ergänzung.
Design-FMEA
Die Design-FMEA (DFMEA) konzentriert sich auf die Entwicklung und Konstruktion eines Produktes und analysiert dessen Produktions- und Montageeignung. Dadurch lassen sich mögliche Risiken identifizieren, die durch ein neues oder verändertes Produktdesign entstehen können. Die DFMEA ist daher vor allem für Unternehmen, die Produkte entwickeln, sehr nützlich.
Sinnvolle FMEA-Ergänzungen können hier die FMEA-MSR bzw. auch die System-FMEA sein.
Doch kein FMEA-Team kann alles allein lösen, um Produkte langfristig erfolgreich zu machen, braucht es eine Strategie für das Produktmanagement. Wie das funktionieren kann, erfahren Sie im Training Strategisches Produktmanagement.
Prozess-FMEA
Die Prozess-FMEA (PFMEA) untersucht potenzielle Schwachstellen in Produktions- und Leistungsprozesse bzw. Prozesse im Allgemeinen. Das Ziel ist die Identifizierung von Fehlerursachen, so dass diese in Form von Fehlernetzen sichtbar werden und das systematische Beheben von Fehlerketten ermöglichen. Prozesse können so nachhaltig optimiert und die vorhandenen Fehlerquellen minimiert werden.
System FMEA oder FMEA-MSR (Monitoring System Response)
Die System-FMEA (S-FMEA untersucht das Zusammenspiel von Teilsystemen in einem Gesamtsystem und legt den Schwerpunkt auf die Analyse der Schnittstellen. Dabei liegt der Fokus auf der Erkennung bzw. der Analyse von Fehlerpotenzialen, die unter Betriebsbedingungen auftreten können. Im Zentrum der Analyse steht die Fragestellung, ob das System bzw. das bedienende Personal in der Lage sind potenzielle Fehler zu erkennen. Das Ziel ist einen sicheren Zustand des Systems während des Kundenbetriebs zu gewährleisten.
Diese FMEA-Art kann ergänzend zur Design-FMEA genutzt werden.
Ob die FMEA als präventiv oder korrektiv betitelt wird, bestimmt ihr Einsatzzeitpunkt
Präventive FMEA
Die Kosten für die Behebung von Fehlern steigen mit der Zeit deutlich. Hier setzt die präventive FMEA an, die den Prozess von Anfang an begleitet und nahezu parallel zu diesem durchgeführt wird. So können Fehler frühzeitig erkannt und behoben werden, was Unternehmen erhebliche Kosten einsparen kann.
Korrektive FMEA
Falls während der Entwicklungsphase keine FMEA durchgeführt wurde, kann eine korrektive FMEA eingesetzt werden. Dabei werden das System und die einzelnen Komponenten rückwirkend analysiert, um Fehlerquellen zu identifizieren. Da diese Methode jedoch viel aufwendiger ist als die präventive Methode, sollte Sie nur in wichtigen Ausnahmefällen durchgeführt werden.
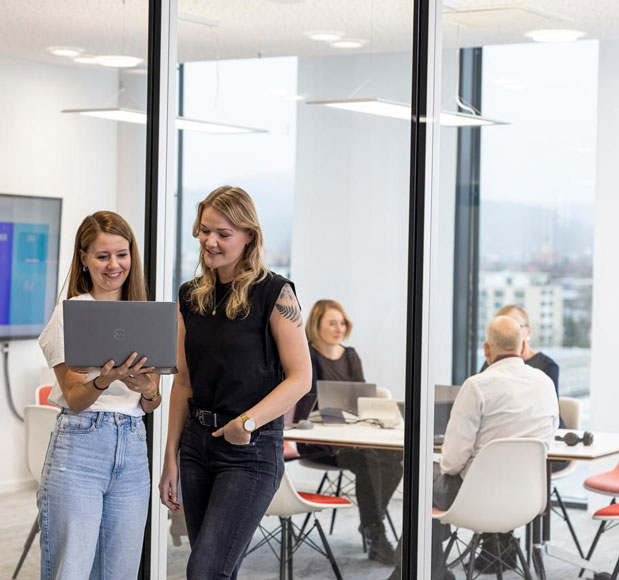
Unsere Empfehlung
Die FMEA Analyse: Qualität steigern & Fehler vermeiden
Das Training ermöglicht Ihnen anhand praxisorientierter Übungen und Fallbeispielen zu erfahren, wie Sie eine FMEA vorbereiteten und durchführen. Lernen Sie, wie Sie potenzielle Fehlerquellen identifizieren und daraus die richtigen Maßnahmen ableiten.
Training: Die FMEA Analyse: Qualität steigern & Fehler vermeiden
Wie läuft eine FMEA ab?
Eine FMEA besteht üblicherweise aus sieben Schritten:
- Planung und Vorbereitung: Festlegung des Umfangs und der Ziele des FMEA-Projekts; Abgrenzung des Produkts und des Prozesses von anderen Systemen
- Strukturanalyse: Analyse der Struktur des Systems, das in der FMEA betrachtet wird
- Funktionsanalyse: Definition der einzelnen Systemelemente und ihrer spezifischen Funktionen
- Fehleranalyse: Identifizierung von möglichen Fehlerquellen, Fehlerarten und Konsequenzen, die sich aus diesen Fehlern ergeben
- Risikoanalyse: Bewertung der Risiken und Konsequenzen, die sich ergeben, wenn der Fehler auftritt und nicht rechtzeitig behoben wird. In diesem Zusammenhang spielt die Risikoprioritätszahl RPZ eine wichtige Rolle.
- Optimierung: Festlegung von Maßnahmen zur präventiven Fehlervermeidung, Umsetzung der Maßnahmen und kontinuierliche Verbesserung des Produkts oder Prozesses.
- Dokumentation der Ergebnisse: Kommunikation der Ergebnisse an die betroffenen Fachbereiche und Schlussfolgerungen aus der FMEA.
Risikoprioritätszahl (RPZ)
Um die Dringlichkeit von Fehlern und Risiken einzustufen, hilft es auf die Risikoprioritätszahl zurückzugreifen. Die Formel lautet wie folgt:
RPZ=B*A*E
Dabei steht A für die Wahrscheinlichkeit des Auftretens eines Fehlers, B für die Bedeutung oder den Grad der Schwere eines Fehlers und E für die Entdeckungswahrscheinlichkeit eines Fehlers. Für die Berechnung der RPZ stufen Sie die drei Faktoren von eins (sehr gering) bis zehn (sehr hoch) ein. Die RPZ kann also maximal bei 1.000 liegen (10 x 10 x 10). Je höher die RPZ ist, desto dringlicher sollten Sie sich mit diesem Fehler oder Risiko befassen.
Die RPZ als alleinige Bewertungszahl zur Priorisierung von Risiken wird allerdings mittlerweile kritisch gesehen, da eine nachvollziehbare Begründung fehlt, wie die möglichen Kombinationen der einzelnen Bewertungsfaktoren (aus denen die RPZ errechnet wird) auszulegen sind.
Eine zuverlässige Priorisierung der Maßnahmen ist damit nicht gegeben bzw. nur mit Unschärfen möglich.
Die neu eingeführte Aufgabenpriorität (eigene Bewertungstabelle der FMEA) ist für die Ableitung der entsprechenden Priorität besser geeignet und folgt einer stringenteren Logik als die RPZ.
Im Ergebnis ist ohnehin jede Organisation angehalten, die FMEA-Bewertungsblätter für den eigenen Kontext kritisch zu prüfen und anzupassen.
Welche Herausforderungen hat eine FMEA?
Die Durchführung von FMEAs ist mit Herausforderungen verbunden, die in der Praxis immer wieder zu beobachten sind.
Die korrekte und damit mehrwertstiftende Anwendung der FMEA erfordert Methodenwissen im Bereich der systematischen Fehleranalyse. Die Kenntnis und Transparenz der zu untersuchenden Prozesse ist eine wichtige Grundlage für eine effektive FMEA. Neben diesen Aspekten kommt hinzu, dass es seitens der Beteiligten eine hohe Bereitschaft braucht „hinter die Kulissen“ zu schauen und Durchhaltevermögen mitzubringen, um Fehler nachhaltig zu eliminieren. Abkürzungen führen hier leider nicht zu einem guten Ergebnis. Das bloße Ausfüllen der FMEA-Formblätter genügt nicht! Das eigentliche Herzstück der FMEA ist die systematische und methodische Analyse von Fehlerketten. Die hier gewonnenen Erkenntnisse sind essenziell wichtig, um geeignete Entdeckungs- und Kontrollmaßnahmen zu etablieren, falls sich Fehlerursachen nicht sofort abstellen lassen.
Die Zielsetzung sollte deshalb lauten: Fehlerursachen rechtzeitig zu erkennen und abzustellen, um Kosten für die Nacharbeitung, den Ausgleich von Reputationsschäden oder im schlimmsten Fall Schadensersatzzahlungen zu vermeiden.
Welche Vor- und Nachteile hat eine FMEA?
Neben den Herausforderungen, die eine FMEA organisatorisch, prozessual und methodisch mit sich bringt gibt es auch zahlreiche Vor- sowie Nachteile, die zu berücksichtigen sind.
Vorteile | Nachteile |
---|---|
Frühzeitige Fehlererkennung -> Dank vorausschauendem Handeln keine Totalausfälle | Hoher personeller und zeitlicher Aufwand |
Bessere Qualitätssicherung durch Reduzierung der Fehlerquote auf ein Minimum | FMEA in Teilen subjektiv -> Risikoeinschätzung ist eine Frage der Perspektive der Experten im Team. Unterschiedliche Einschätzungen können zu Fehlern bei der Bewertung und Priorisierung von Risiken führen. |
Niedrigere Kosten durch frühzeitige Fehlerbehebung | |
Nachhaltige Fehlerbehebung durch Prozessoptimierung | |
Lückenlose Dokumentation von Risiken und Gegenmaßnahmen |
Aus wem besteht das FMEA Team?
Das FMEA Team kann man sich als Kreis vorstellen. In der Mitte steht der FMEA Moderator. Diese Rolle erfordert nicht nur ein breites Fach- und Methodenwissen, sondern auch den Blick für das große Ganze. Seine Aufgabe ist es, das gesamte Projekt zu überblicken. Er unterstützt bei der Planung, Durchführung und Nachbereitung. Er ist auch dafür verantwortlich, das Team zusammenzustellen und einen groben Zeitplan zu erstellen. Manchmal ist der FMEA Moderator nicht Teil des eigentlichen Projektteams – in diesem Fall spricht man von einem externen Moderator.
Einen Schritt weiter im Kreis befindet sich das Kernteam. Hier stehen Mitarbeiter, die direkt am Projekt oder Prozess beteiligt sind und ihr Wissen einbringen. Es ist aber auch wichtig, Experten mit ausreichendem Fach- und Methodenwissen in dieses Team einzubinden. So kann sichergestellt werden, dass der Prozess erfolgreich verläuft.
Den äußersten Kreis bildet das so genannte erweiterte Team. Hier sind weitere Mitarbeiter aus Produktion, Qualitätsmanagement und Kundendienst vertreten. Sie liefern zusätzliche Informationen, die dem FMEA Team helfen, fundierte Entscheidungen zu treffen.
Besuchen Sie auch unser Seminar „Qualitätsmanagement in der Praxis“, um alle wichtigen Grundlagen zum Thema Qualitätsmanagement zu erlernen.
Wie kann ein FMEA-Workshop ablaufen?
In der Praxis haben sich moderierte FMEA-Workshops bewährt. Moderiert deshalb, weil sich die strukturierte und systematische Vorgehensweise (7 Schritte) als vorteilhaft erwiesen hat und mit Hilfe eines Moderators (idealerweise ein FMEA-Moderator) sichergestellt wird, dass die Abfolge eingehalten wird. Ein (externer oder interner) Moderator kann auch nützlich sein, um die Produkt- und Prozessexperten methodisch „zu entlasten“, so dass sich diese auf potenzielle Fehlerquellen fokussieren können. Auch kann ein Moderator kritische Fragen ermöglichen, Diskussionen fördern und diese auf ein Ergebnis hinsteuern.
Neben der Moderationskompetenz ist eine gute Vorbereitung die halbe Miete. Hierzu zählt neben einer Auftragsklärung und Zielformulierung auch die Bereitstellung relevanter Unterlagen zu Produkten und Prozessen, die methodische Vorbereitung eines FMEA-Workshops, die Klärung von Verfügbarkeiten von Teilnehmenden, die Terminbuchung und ggf. noch die Auswahl von geeigneten Kandidatinnen für die Moderation des Workshops.
Empfehlenswert ist auch die Einladung von „fachfremden“ KollegInnen, die oftmals sehr interessante Fragen stellen, die das Hinterfragen von Abläufen ermöglichen.
Wichtige (und oft vergessene) Aufgabe einer jeden Organisation ist jedoch die Erstellung von eigenen Bewertungsblättern für das eigene Produkt! Hier erweist sich der Produktionsstandard nicht immer als passgenau auf die eigenen Produktlandschaft. Dies gilt nicht für die Bewertungsblätter für die Prozesse. Diese lassen sich analog für die eigenen Prozesse einsetzen. Die Bewertungsblätter, die als Standard zur Verfügung gestellt werden sollten jedoch mindestens auf Anwendbarkeit geprüft und dann angepasst werden.
Aus Gründen der besseren Lesbarkeit wird im Beitrag auf die gleichzeitige Verwendung weiblicher und männlicher Sprachformen verzichtet und das generische Maskulinum verwendet. Sämtliche Personenbezeichnungen gelten gleichermaßen für alle Geschlechter.
FAQS: FMEA
Was ist eine FMEA?
Eine FMEA (Fehlermöglichkeits- und Einflussanalyse) ist eine systematische Methode, um potenzielle Fehler und Risiken in Produkten, Prozessen oder Systemen zu identifizieren und zu bewerten. Sie hilft, Sicherheit zu gewährleisten, Qualität zu sichern, Kosten zu sparen und Fehler- sowie Garantiekosten zu minimieren.
Welche Arten von FMEA gibt es?
Es gibt drei Hauptarten von FMEA: System-FMEA (SFMEA), die sich auf das gesamte System konzentriert; Design-FMEA (DFMEA), die den Designprozess eines Produkts analysiert; und Prozess-FMEA (PFMEA), die sich auf den Produktionsprozess konzentriert.
Wie läuft FMEA ab?
Eine FMEA durchläuft sieben Schritte: Planung und Vorbereitung, Strukturanalyse, Funktionsanalyse, Fehleranalyse, Risikoanalyse, Optimierung und Dokumentation der Ergebnisse. Diese Schritte helfen, potenzielle Fehlerquellen systematisch zu erkennen und Maßnahmen zur Fehlervermeidung zu implementieren.
Was versteht man unter der Risikoprioritätszahl (RPZ)?
Die RPZ ist ein Maß für die Dringlichkeit von Fehlern und Risiken und wird durch Multiplikation der Wahrscheinlichkeit des Auftretens eines Fehlers, der Bedeutung des Fehlers und der Entdeckungswahrscheinlichkeit des Fehlers berechnet. Die drei Faktoren werden von 1 bis 10 eingestuft, sodass die RPZ bei maximal 1.000 liegen kann. Die RPZ allein ist jedoch nicht immer verlässlich, da die Interpretation der Faktorenkombinationen unklar sein kann.
Welche Vor- und Nachteile hat die Anwendung einer FMEA?
Vorteile der FMEA umfassen frühzeitige Fehlererkennung, verbesserte Qualitätssicherung und niedrigere Kosten durch Fehlervermeidung. Nachteile können ein hoher personeller und zeitlicher Aufwand sowie subjektive Risikoeinschätzungen sein.
Aus wem besteht ein FMEA-Team?
Ein FMEA-Team besteht typischerweise aus einem Moderator, der das Projekt überblickt, einem Kernteam aus direkt beteiligten Mitarbeitern und Experten sowie einem erweiterten Team aus weiteren Mitarbeitern, die zusätzliche Informationen liefern.